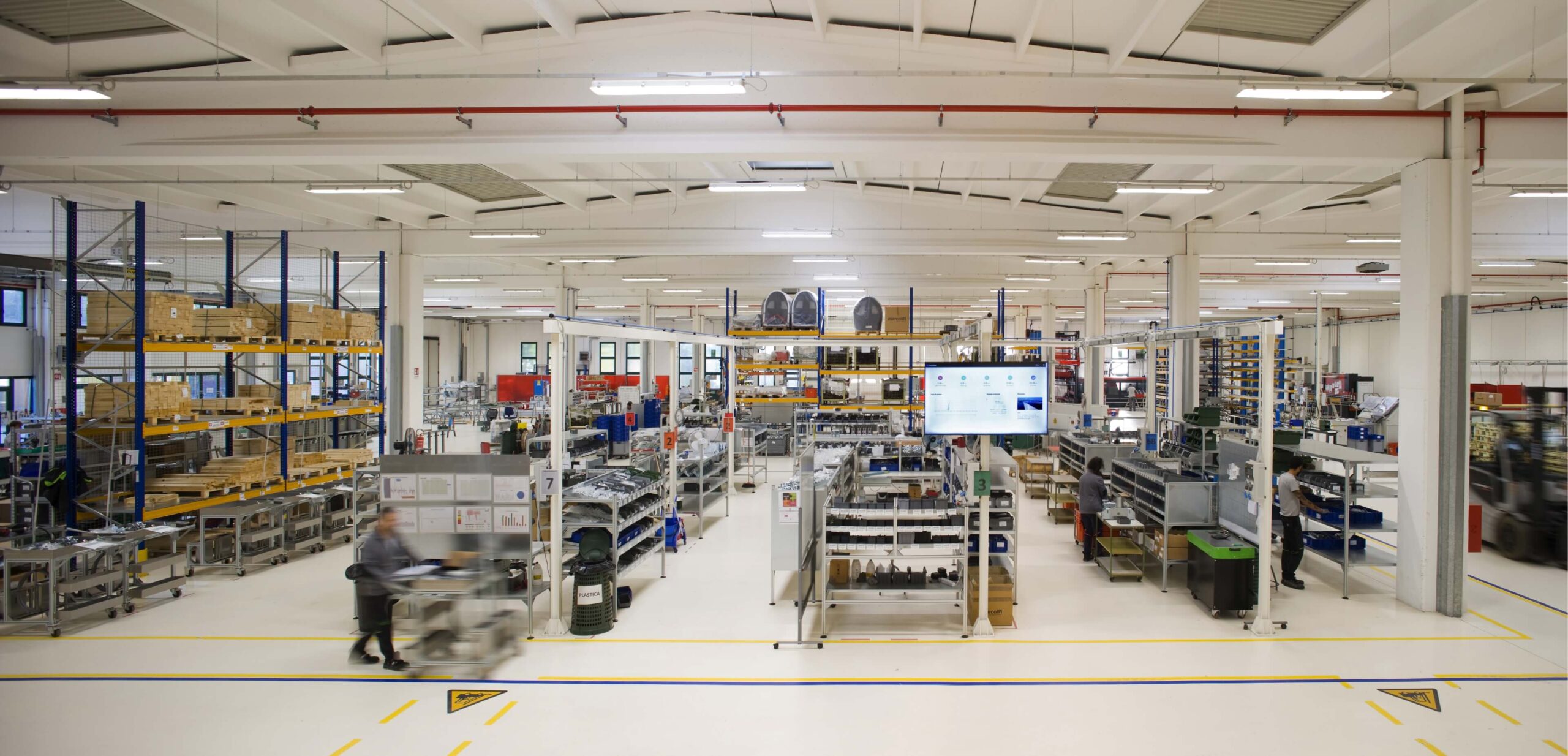
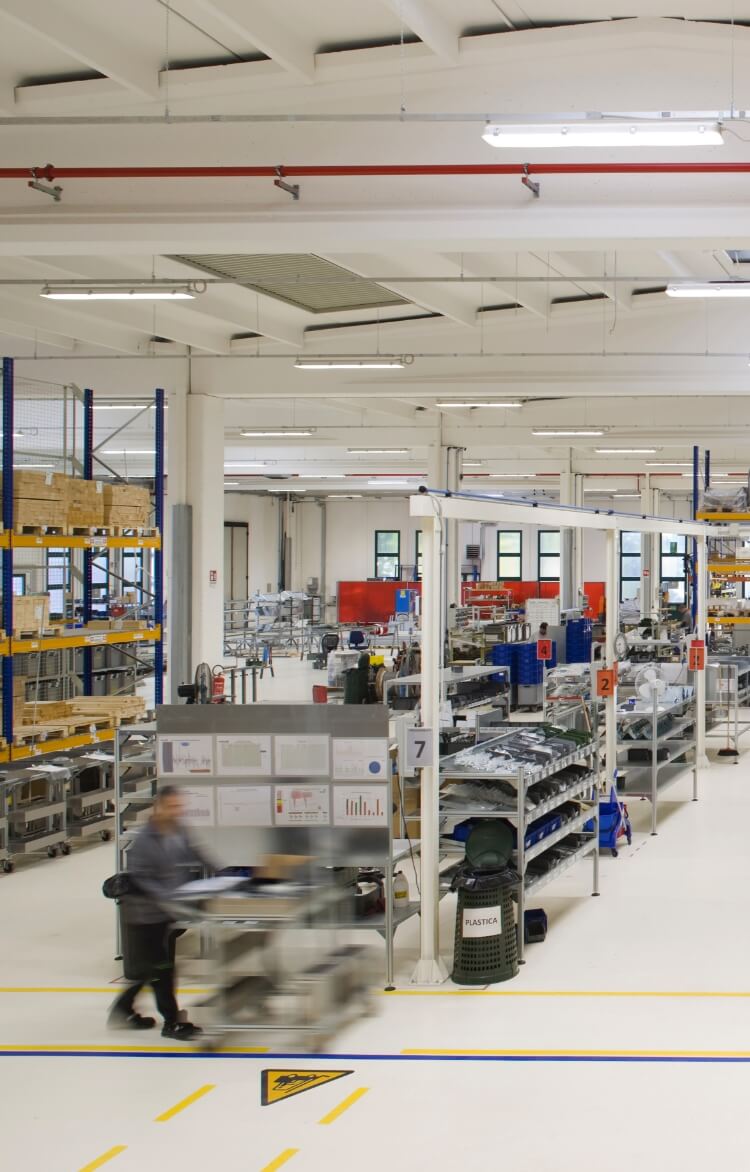
Lean System: Redesigning
business processes through
cultural change.
Since 2019, we’ve embarked on a comprehensive lean transformation across all company processes: delivery, demand, development, service, and deployment, to support growth with a scientific method. This lean approach has significantly reduced delivery times and improved costs and quality.
Lean processes aren’t just a scientific method but a systemic investment in resources.
The Lean system, a streamlined organisation of processes inspired by Toyota Production System’s efficiency and innovation study, has become a global benchmark for businesses.
We adopted lean principles by redesigning our company layout and then tackling a radical cultural change throughout the organisation. Today, we can claim to BE a lean company, not just DO lean, as we don’t merely apply techniques and tools. Rather, lean principles are now an intrinsic part of our corporate mindset at all levels.
The Lean system also means greater sustainability by reducing time, inventory, defects, and non-value activities. This leads to a greater respect for the environment, while achieving set goals with fewer resources.
Lean System: the Marcolin Covering results.
Multidisciplinary teams, Agile PM and Scrum method: Everyone collaborates to contribute to continuous improvement.
Multidisciplinary teams work on each Marcolin Covering project to offer broader insights into problems and solutions.
Marcolin Covering employs the Agile Project Management System, based on iterative and incremental principles that foster collaboration and continuous value creation for the customer.
Alongside this approach, Scrum methodologies enhance the skills of each component of these multidisciplinary teams, promoting continuous improvement in process, service, and product management, embodying lean system principles.
Investing in people.
OF OUR PERSONNEL
IN 10 YEARS
INDEX
FOR NEW HIRES
CLASSROOM TRAINING
Being lean.
Being lean to us means we’ve internalised the principles, learned to consciously use techniques and tools, and become an example for businesses looking to improve their processes.
We host companies and students, recognising the importance of spreading knowledge of lean principles to new generations.
With auxiell’s support throughout this transformation, we now feel ready to become a role model:
“Being an example means putting yourself out there, not fearing mistakes, and taking responsibility.”
auxiell
auxiell Case History: Marcolin lean system, aspiring to be a virtuous example.
From reorganising the first production plant to streamlining all the organisation’s macro-processes, these are the results of Marcolin Covering’s lean transformation.
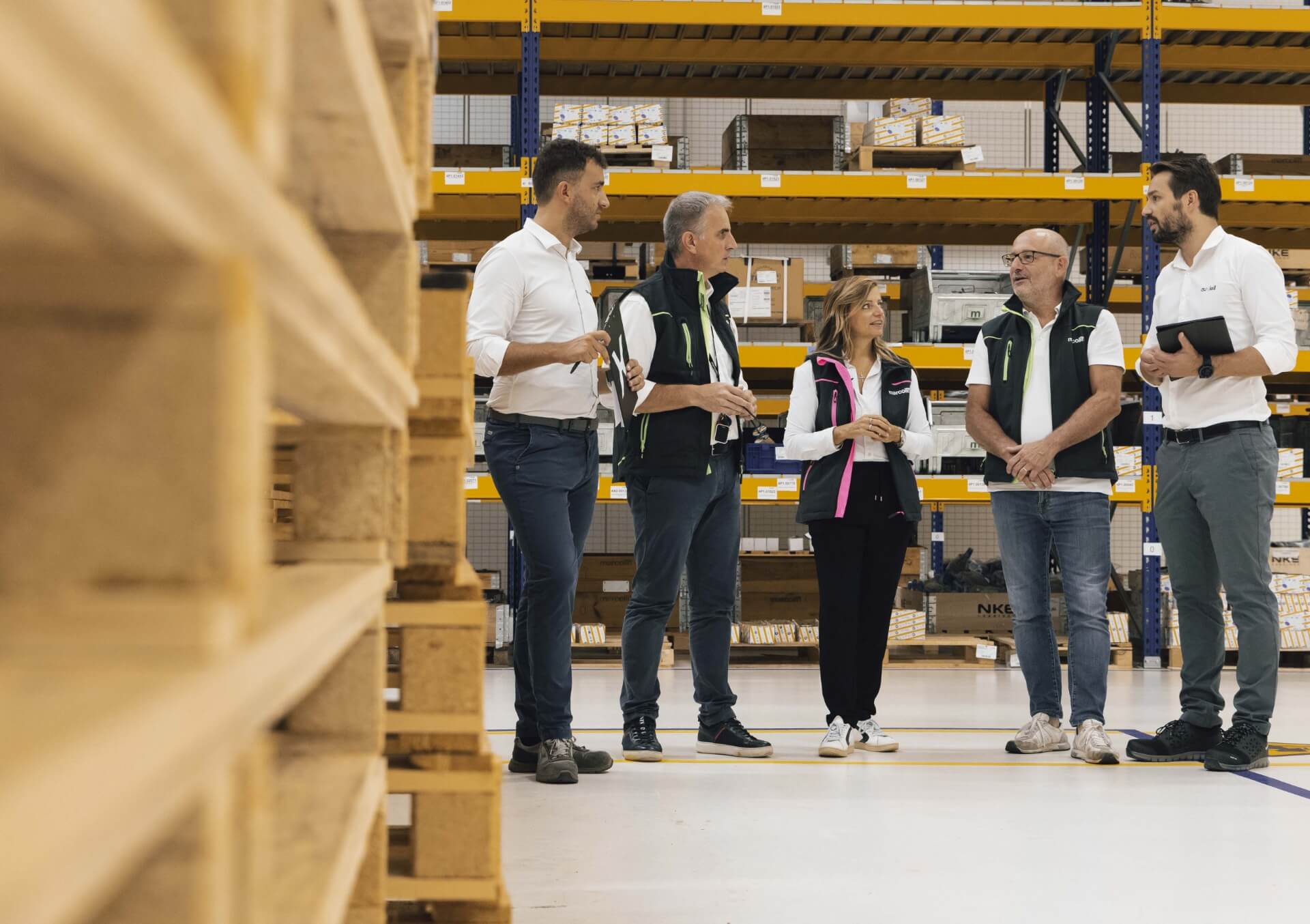
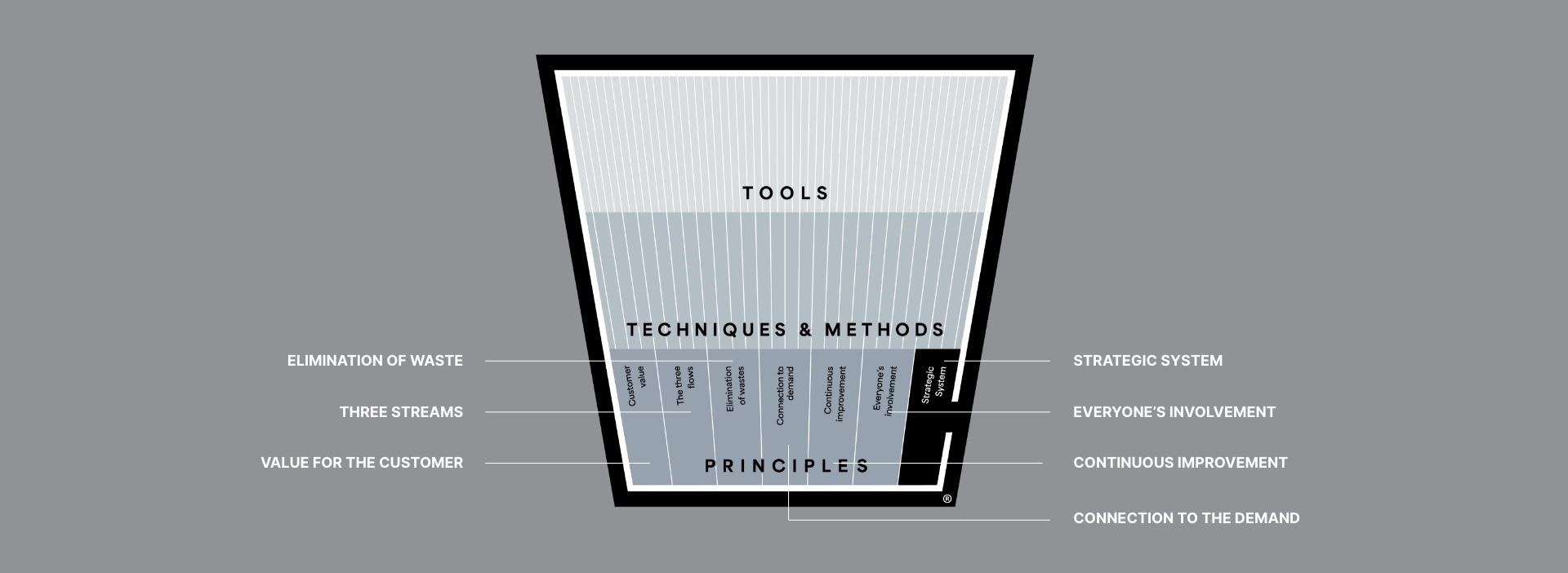
SPDCA scientific approach.
The company must enhance customer value by focusing not only on product and service aspects but also on process organisation, creating a virtuous cycle of flexibility, focus and continuous improvement. This was achieved through the SPDCA (Scan, Plan, Do, Check, Act) scientific approach.
- SCAN
Analyse the context to define the current state and identify waste and opportunities. - PLAN
Search for the root cause, identify countermeasures and draw up the action plan. - DO
Perform the planned tasks in line with the action plan. - CHECK
Verify that the activities have been carried out in line with the plan and that the objectives have been achieved. - ACT
Standardize the new method and apply it to processes.
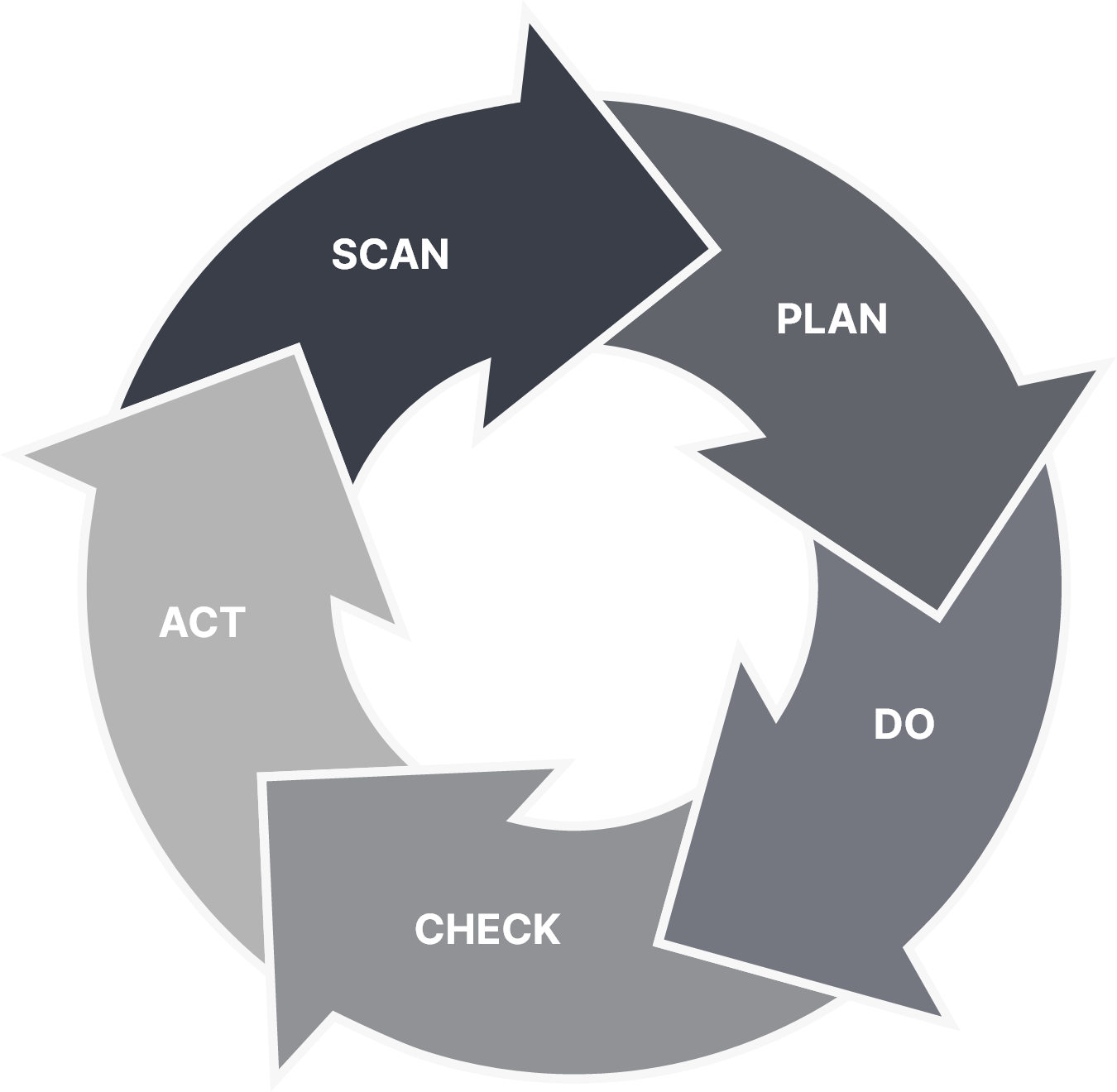
GO SEE/
ASK WHY/
SHOW RESPECT
Fujio Cho (President of Toyota)
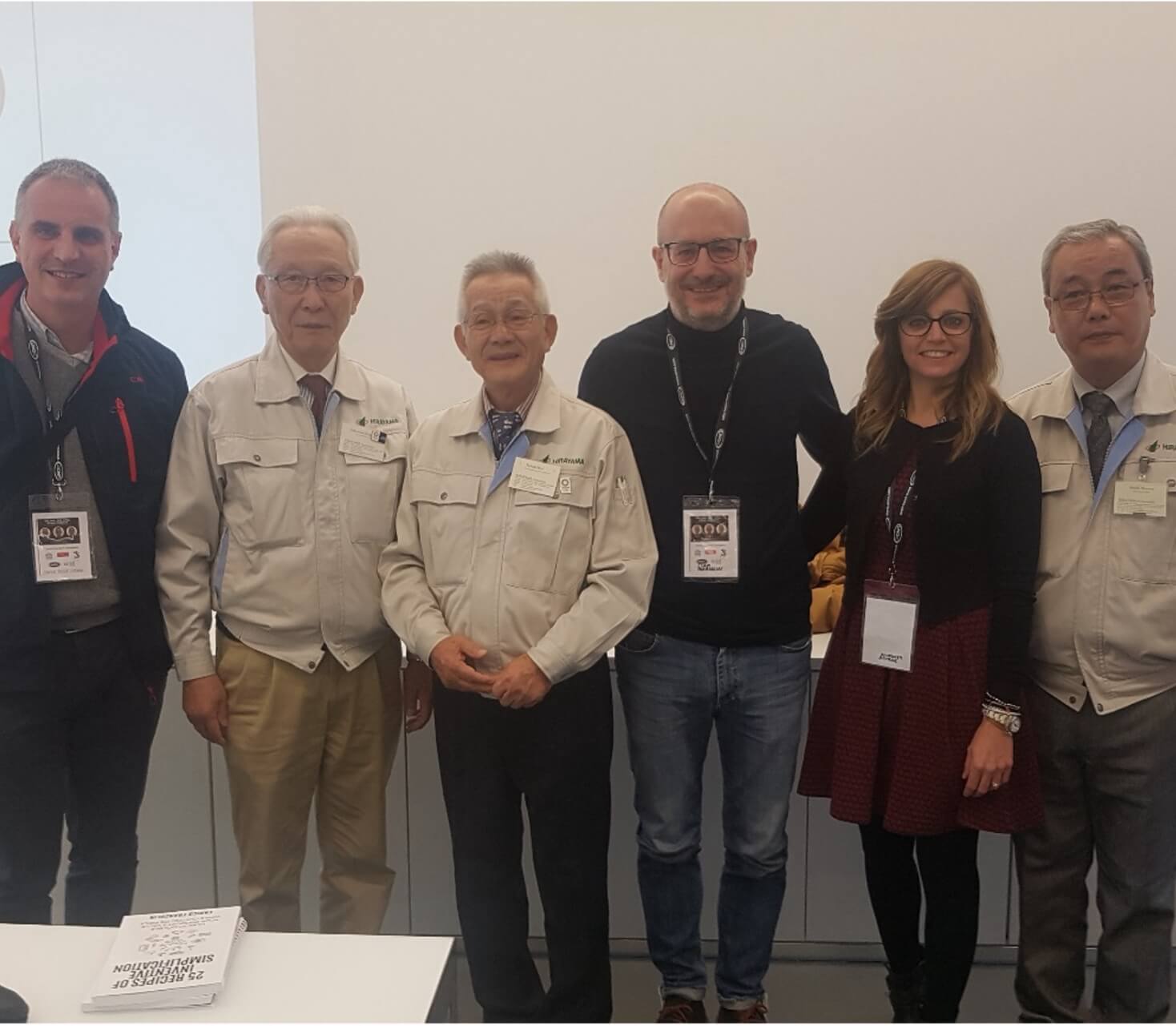
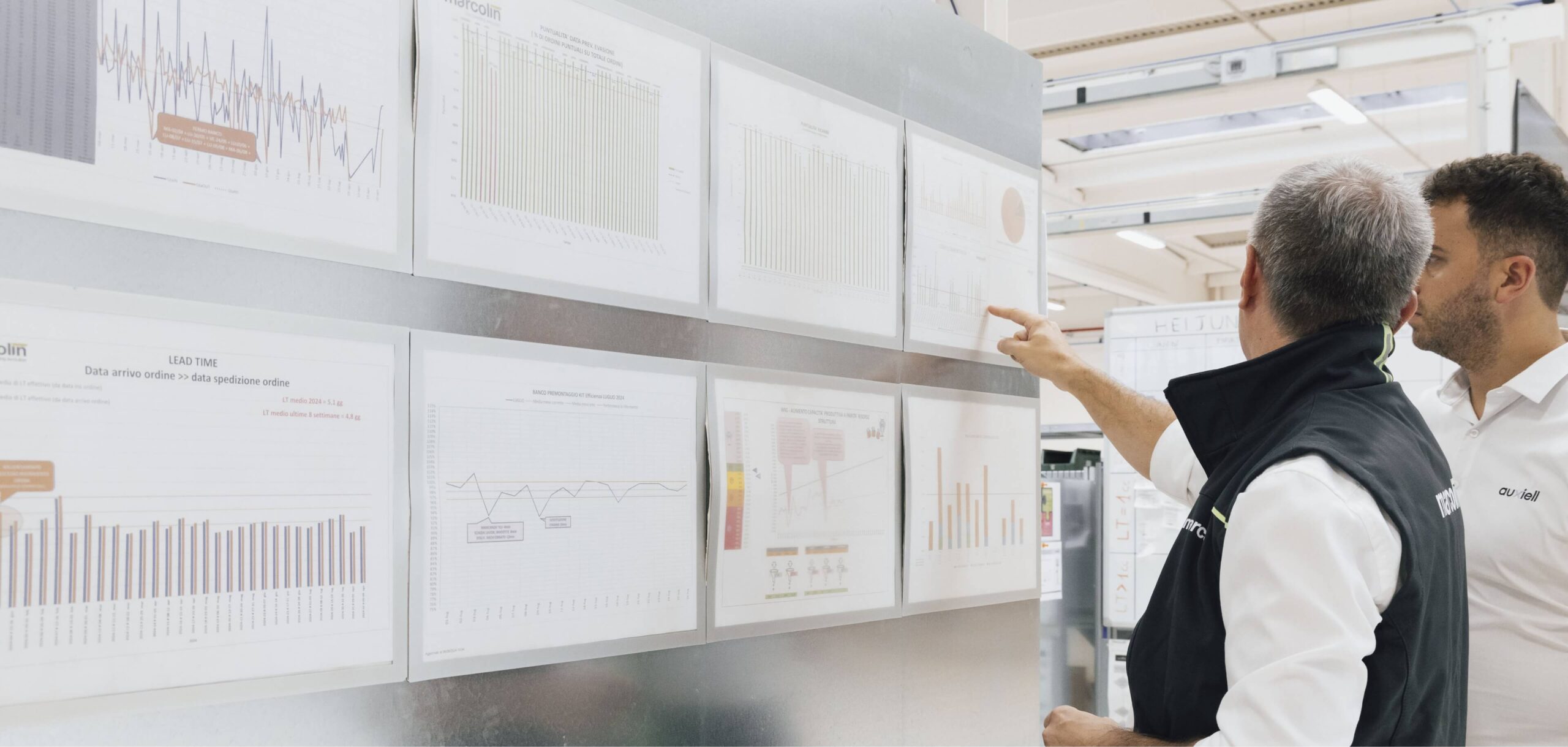